Ever heard of absorption chillers? They’re cooling systems that utilize heat sources instead of electricity to produce chilled water for air conditioning and refrigeration. Let’s get to know more about this technology.
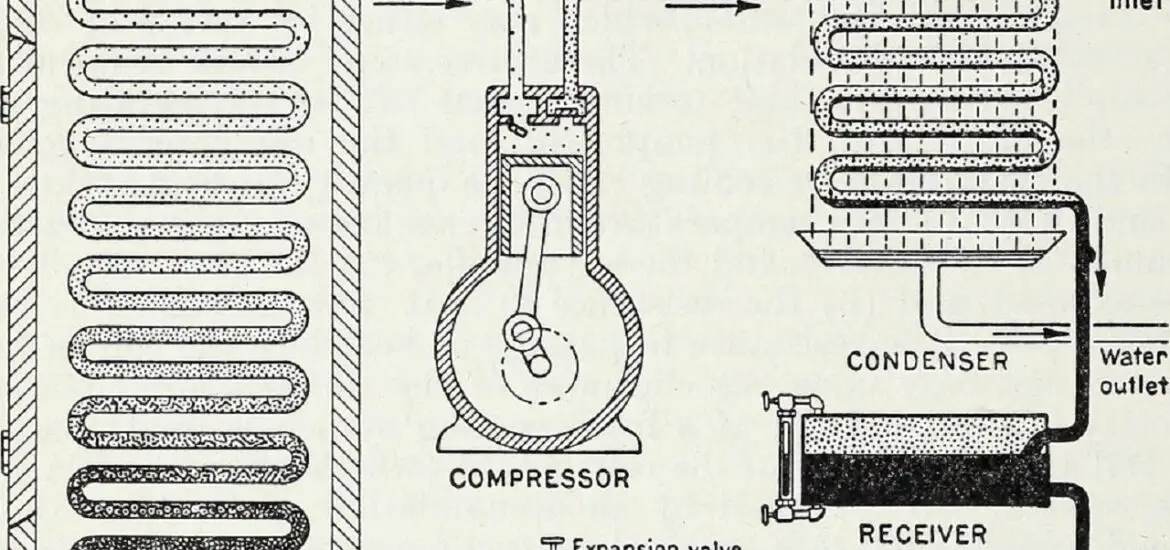
Table of Contents
Definition of Absorption Chillers
These chillers are a type of refrigeration system that uses a heat-driven process, involving a refrigerant and an absorbent, to provide cooling.
Components of Absorption Chillers
These chillers have five main components: evaporator, absorber, generator, condenser, and expansion valve. They work together to create a cooling effect.
Applications of Absorption Chillers
From large-scale industrial plants to residential buildings, these chillers cater to various cooling needs with minimal environmental impact.
In Absorption Chiller, the Working Medium Used Is
Overview of Working Mediums
The working mediums in absorption chillers are a combination of refrigerants and absorbents that interact to produce the cooling effect.
Absorption Refrigerants
Refrigerants are substances that change phase (evaporate and condense) to absorb and release heat, providing cooling. Common refrigerants include water and ammonia.
Absorbents
Absorbents are substances that attract and hold the refrigerant. Lithium bromide and water are commonly used absorbents.
Common Working Medium Pairs
There are two popular pairs of working mediums: water-ammonia and water-lithium bromide. Each has its pros and cons, depending on the application.
Water-Ammonia
The water-ammonia pair is commonly used in industrial applications due to its high temperature range and ability to work with lower heat sources.
Water-Lithium Bromide
Water-lithium bromide is favored in commercial and residential applications due to its non-toxic and non-flammable properties.
Absorption Chiller Working Principle
Overview of the Working Principle
Key Components in the Working Principle
Each of the five main components – evaporator, absorber, generator, condenser, and expansion valve – play a crucial role in the cooling process.
Evaporator
The evaporator is where the refrigerant absorbs heat and evaporates, producing chilled water for cooling purposes.
Absorber
In the absorber, the refrigerant vapor is absorbed by the absorbent, creating a concentrated solution.
Generator
The generator heats the concentrated solution, separating the refrigerant vapor from the absorbent.
Condenser
The condenser cools the refrigerant vapor, transforming it into a liquid, which is then sent to the expansion valve
Expansion Valve
The expansion valve reduces the pressure of the liquid refrigerant, causing it to evaporate and absorb heat, starting the cycle again.
Thermodynamics of Absorption Chillers
Understanding the heat and mass transfer processes and the coefficient of performance (COP) is essential for evaluating the efficiency of these chillers.
Heat and Mass Transfer
Heat and mass transfer processes occur at different stages of the absorption chiller cycle, ensuring the continuous flow of the working medium.
Coefficient of Performance (COP)
The COP measures the efficiency of these chillers, comparing the cooling effect produced to the amount of heat input required.
How Absorption Chiller Works
Step-by-Step Process
The absorption chiller’s cooling process involves evaporation, absorption, desorption (regeneration), condensation, and expansion.
Evaporation
Refrigerant absorbs heat, evaporates, and cools the water in the evaporator.
Absorption
The refrigerant vapor is absorbed by the absorbent in the absorber, forming a concentrated solution.
Desorption (Regeneration)
The generator heats the concentrated solution, releasing refrigerant vapor and regenerating the absorbent.
Condensation
Refrigerant vapor is cooled and condensed back into a liquid in the condenser.
Expansion
The expansion valve lowers the pressure of the liquid refrigerant, allowing it to evaporate and restart the cooling cycle.
Heat Sources for Absorption Chillers
These chillers use a variety of heat sources, including waste heat, solar energy, geothermal energy, and natural gas, making them versatile and sustainable.
Waste Heat
Waste heat from industrial processes or power plants can be harnessed to power absorption chillers, reducing energy consumption and emissions.
Solar Energy
Solar collectors can provide heat to drive absorption chillers, offering an eco-friendly and renewable cooling solution.
Geothermal Energy
Heat from the earth’s core can be used to power absorption chillers, creating a sustainable and continuous source of energy.
Natural Gas
Natural gas-fired absorption chillers offer high efficiency and reliability, making them a popular choice for many applications.
Absorption Chiller Explained
Advantages of Absorption Chillers
These chillers offer several benefits, including energy efficiency, environmental benefits, and low noise and vibration levels.
Energy Efficiency
By utilizing heat sources instead of electricity, absorption chillers can save energy and reduce operational costs.
Environmental Benefits
With minimal greenhouse gas emissions and the ability to use renewable energy sources, absorption chillers are an eco-friendly cooling option.
Low Noise and Vibration
These types of chillers operate quietly, making them ideal for noise-sensitive environments like hospitals and residential areas.
Disadvantages of Absorption Chillers
Despite their advantages, these chillers have some drawbacks, including high initial costs, maintenance and operating costs, and limited cooling capacity.
High Initial Costs
These chillers can be more expensive upfront than traditional vapor compression chillers, making them less attractive for some applications.
Maintenance and Operating Costs
Regular maintenance and the need for specialized personnel can increase the operating costs of absorption chillers.
Limited Cooling Capacity
Compared to vapor compression chillers, absorption chillers may have a lower cooling capacity, which could limit their use in certain situations.
Read our other articles on absorption refrigeration – Absorption Refrigeration: Easy Guide to Understanding It
Absorption Chiller Basics
Comparison with Vapor Compression Chillers
Absorption and vapor compression chillers differ in their working principles and performance characteristics.
Working Principle Differences
While absorption chillers use a heat-driven process, vapor compression chillers rely on mechanical compression to generate cooling.
Performance Differences
Absorption chillers generally have lower cooling capacities and COP values compared to vapor compression chillers but offer environmental and operational advantages.
Types of Absorption Chillers
There are three main types of these chillers: single-effect, double-effect, and triple-effect chillers, each offering varying levels of efficiency and complexity.
Single-Effect Absorption Chillers
These chillers use a single heat source and have relatively low COP values. They are simpler and less expensive than other types.
Double-Effect Absorption Chillers
Double-effect chillers utilize two heat sources, resulting in higher COP values and improved efficiency compared to single-effect chillers.
Triple-Effect Absorption Chillers
Triple-effect chillers use three heat sources, offering the highest COP values and efficiency among these chiller types but are more complex and costly.
Absorption Refrigeration Machines
Industrial Applications
Absorption chillers are widely used in various industries, including food and beverage, chemical and pharmaceutical, and HVAC systems in large buildings.
Food and Beverage Industry
These chillers provide efficient cooling for food processing, storage, and preservation, helping maintain product quality and safety.
Chemical and Pharmaceutical Industry
These chillers are also used in the chemical and pharmaceutical industry to maintain precise temperature and humidity levels during manufacturing processes.
HVAC Systems in Large Buildings
Large commercial and residential buildings can benefit from these chillers for efficient, quiet, and environmentally friendly air conditioning.
Residential Applications
Though less common, these chillers can also be used in residential settings, providing quiet and energy-efficient cooling.
Absorption Chiller Operation
Operating Parameters
Temperature, pressure, and heat source selection are essential parameters to consider when operating these chillers.
Temperature and Pressure
Maintaining optimal temperature and pressure conditions is crucial for efficient operation and performance of these types of chillers.
Heat Source Selection
Choosing the right heat source for this type of chiller can significantly impact its efficiency, environmental footprint, and operational costs.
Control Strategies
Implementing effective control strategies, such as load control, chilled water temperature control, and refrigerant concentration control, is essential for optimal chiller performance.
Load Control
Managing the cooling load ensures that the absorption chiller operates efficiently and meets the desired cooling requirements.
Chilled Water Temperature Control
Controlling the temperature of chilled water helps maintain the desired cooling effect and improves overall system performance.
Refrigerant Concentration Control
Regulating the refrigerant concentration in the working medium is crucial for the smooth operation and efficiency of the absorption chiller.
Absorption Chiller Principle
Key Concepts in the Principle
Understanding the solution concentration, heat and mass transfer, and refrigerant boiling points is essential to comprehend the absorption chiller principle.
Solution Concentration
The concentration of the refrigerant-absorbent solution directly affects the chiller’s performance and thermodynamic properties.
Heat and Mass Transfer
Heat and mass transfer processes play a crucial role in the operation of these chillers, ensuring the continuous circulation of the working medium.
Refrigerant Boiling Points
The boiling points of refrigerants significantly impact the chiller’s performance, as they determine the amount of heat required for evaporation and condensation processes.
Thermodynamic Cycles
Single-effect, double-effect, and triple-effect absorption cycles are the main thermodynamic cycles used in absorption chillers, each offering different levels of efficiency.
Single-Effect Absorption Cycle
This cycle involves a single heat source, and while it is less efficient than other cycles, it is simpler and more cost-effective.
Double-Effect Absorption Cycle
Using two heat sources, the double-effect cycle offers improved efficiency and higher COP values compared to the single-effect cycle.
Triple-Effect Absorption Cycle
The triple-effect cycle, with three heat sources, boasts the highest efficiency and COP values but is more complex and expensive.
Conclusion
Future Developments in Absorption Chillers
Advancements in materials, novel working medium pairs, and increasing adoption of these types of chillers are expected to shape the future of this technology.
Advanced Materials
Developing new materials with enhanced thermal and chemical properties could significantly improve the efficiency and performance of these chillers.
Novel Working Medium Pairs
Exploring new combinations of refrigerants and absorbents may lead to more efficient and environmentally friendly absorption chillers.
Increasing Adoption of Absorption Chillers
Regulatory incentives and energy efficiency targets are expected to drive the increased adoption of these chillers in various sectors.
Regulatory Incentives
Government policies and incentives promoting energy-efficient technologies may encourage more industries to adopt more of these types of chillers.
Energy Efficiency Targets
As industries strive to achieve their energy efficiency goals, the demand for these types of chillers is likely to grow.