When you think of “underground refrigerant piping detail,” what comes to mind? Likely, a complex network of pipes beneath our feet, quietly and efficiently controlling the temperature of our homes and businesses. This hidden labyrinth is vital to many HVAC systems, and this article is going to give you an in-depth look at its ins and outs, from installation to maintenance and common issues.
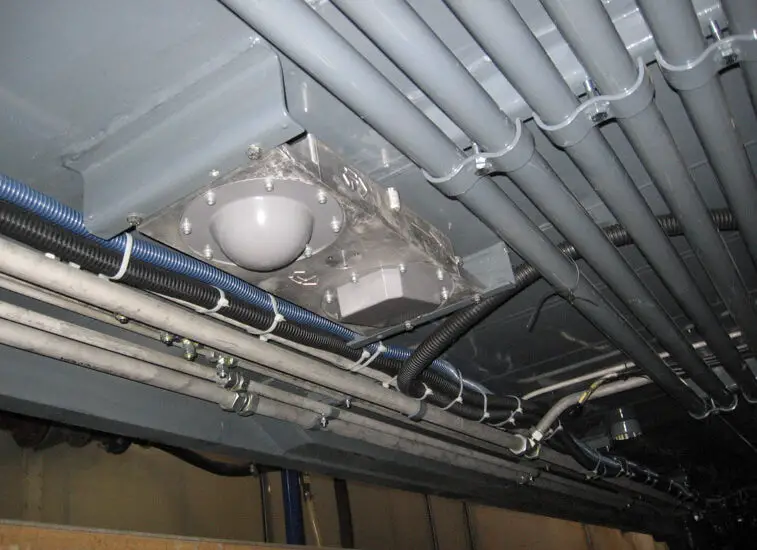
Table of Contents
Understanding Underground Refrigerant Piping Detail
So, what’s the big deal about these pipes, anyway?
Definition and Purpose of Underground Refrigerant Piping
First things first, let’s talk about what this piping actually is and why it’s so important. Underground refrigerant piping is the network of pipes installed underground that transport refrigerants—substances used in the cooling mechanism of air conditioning systems. The pipes connect different parts of the HVAC system and help in heat exchange, playing a vital role in maintaining the system’s efficiency.
Role in HVAC Systems
These underground pipes aren’t just for decoration—they serve a critical purpose in HVAC systems. In HVAC systems, these underground pipes transport refrigerants from the outdoor unit to the indoor evaporator coil, facilitating the cooling or heating process. Any leaks or issues with these pipes can significantly affect the system’s performance.
Types of Refrigerants Used
Several types of refrigerants can be used in these systems, including but not limited to R-22, R-410A, R-32, and R-134a. The type of refrigerant used will depend on the specific requirements of the HVAC system, environmental considerations, and local regulations.
Components of Underground Refrigerant Piping
These consist of the pipe material itself (often copper, but can also be steel or plastic), insulation to maintain temperature consistency, joints and connections, and protective casings or conduits.
Pipe Material and Insulation
The material for the pipes should be durable and resistant to corrosion, with copper being a popular choice. Insulation is crucial for maintaining the temperature of the refrigerant and improving overall system efficiency.
Pipe Size and Length Considerations
Size matters when it comes to piping. Let’s delve into why. Pipe sizing is crucial to prevent pressure loss and ensure the HVAC system can meet the heating and cooling requirements of the building. The length of the pipe runs also factors into this, as longer runs can reduce system efficiency.
Installation Details for Underground Refrigerant Piping
Now that we’ve covered the basics, let’s talk about the nitty-gritty: installation.
Pre-Installation Planning
Effective pre-installation planning involves setting clear objectives, defining the scope of work, and acquiring necessary tools. Understanding the project’s requirements, mapping out the timeline, and identifying potential challenges can result in a smoother process.
Site Assessment
Assess the site to determine soil conditions, potential obstructions like existing utility lines, and the most efficient pipe route. This evaluation helps avoid complications during the excavation and installation stages.
Selecting the Right Pipe Material and Size
The correct pipe material and size are crucial for optimal system performance. For underground refrigerant piping, choose materials like copper or plastic that can withstand temperature changes and corrosion. Ensure the size matches the capacity of the cooling system.
The Installation Process
This involves detailed steps including excavation, pipe laying, and post-installation testing. Following the correct sequence and applying good workmanship ensures longevity of the refrigerant piping system and maintains its efficiency.
Excavation and Trenching
Carefully excavate and trench the soil to create a space for your pipes. Trenches should be wide and deep enough to accommodate the pipe and insulation, typically around 24-30 inches deep.
Laying and Connecting the Pipes
Next, carefully lay the pipes in the trench, ensuring they’re level and correctly oriented. Connect the pipes using appropriate fittings and ensure they’re properly sealed to prevent leaks.
Testing for Leaks and Insulation
After installation, it’s crucial to test for leaks using a pressure test. Also, inspect the insulation to ensure it’s intact and provides enough thermal resistance to protect the pipe from temperature extremes.
Maintenance of Underground Refrigerant Piping
Installation is just the beginning. To keep your system running smoothly, regular maintenance is key. Regular inspections should be carried out to detect leaks, assess insulation condition, and clean/repair as necessary. Regular maintenance prevents issues from escalating and prolongs the system’s lifespan.
Regular Inspections
Conduct regular inspections of your refrigerant piping system. This includes checking for signs of leaks, verifying the condition of insulation, and ensuring pipes are secure. Regular inspections can identify potential issues early, saving time and money.
Leak Detection
Early leak detection minimizes damage and system inefficiency. Look for oil stains, abnormal icing, or gas bubbles in standing water. Also consider using electronic leak detectors for more precise detection.
Insulation Checks
Examine insulation regularly for signs of wear, dampness, or damage. Efficient insulation is vital to maintain optimal pipe temperatures and system efficiency. Poor insulation can lead to higher energy costs and equipment strain.
Cleaning and Repair
Clean pipes periodically to prevent blockages. If any damages or leaks are discovered during inspection, repair them promptly. Timely repairs prevent minor issues from escalating into major problems.
Dealing with Blockages
Identify blockages through decreased system efficiency or inspections. Use pipe cleaning tools to remove blockages, ensuring free flow of refrigerant. If a blockage persists, seek professional help.
Repairing Leaks and Damages
Repair leaks immediately to prevent system inefficiency and environmental harm. Methods can include soldering for minor leaks or pipe replacement for major damages. Always use proper safety measures during repairs.
To read more in-depth articles about refrigerants, click here: Articles on Refrigerants: The Ultimate Guide to Understanding Them
Common Issues with Underground Refrigerant Piping
Even with regular maintenance, issues can arise. Here are some of the most common ones. Some common issues include leaks, insulation failures, and blockages. Each of these can significantly affect the HVAC system’s efficiency and longevity.
Leaks and Damages
Leaks and damages often result from improper installation, material degradation, or external factors like soil movement. These can lead to refrigerant loss and system inefficiency.
Causes of Leaks
Leaks may occur due to corrosion, poor connections, physical damage, or natural wear and tear. Regular maintenance can mitigate these risks.
Impacts of Leaks on System Efficiency
Leaks can result in refrigerant loss, reducing the system’s cooling capacity and efficiency. This increases energy usage and can shorten equipment lifespan.
Insulation Failures
Insulation failures, caused by damage or wear and tear, can lead to energy loss, system inefficiency, and higher operating costs.
Causes of Insulation Failure
Insulation can fail due to moisture intrusion, improper installation, rodent damage, or natural deterioration over time.
Implications of Insulation Failure
Insulation failure can result in energy loss as heat transfer increases. This reduces system efficiency, leading to higher energy consumption and costs.
Best Practices for Underground Refrigerant Piping
Now that we’ve covered the common issues, let’s talk about how to avoid them. Best practices include selecting suitable materials based on local soil conditions, ensuring proper depth and slope during installation, regular inspections, and prompt repairs.
Selection of Materials
Opt for durable, corrosion-resistant materials suitable for underground refrigerant pipes like copper or specific types of plastic. These materials can withstand fluctuating temperatures and pressure, minimizing the risk of leaks and damages.
Optimal Pipe Materials for Different Soils
The soil type can affect pipe material choice. For example, plastic is better in acidic soil, while copper performs well in most soil conditions. Assess local soil composition before making your choice.
Choosing the Right Insulation
Select insulation that’s moisture-resistant and provides excellent thermal resistance, like closed-cell foam. Ensure it suits the pipe material and surrounding environmental conditions.
Installation Techniques
Follow best practices in installation, such as ensuring pipes have sufficient depth and slope, and connections are sealed properly. This reduces future maintenance requirements and enhances system efficiency.
Ensuring Proper Depth and Slope
Pipes should be deep enough to avoid freeze-thaw cycles, typically 24-30 inches. A slight slope allows for condensate drainage, preventing water accumulation that could damage pipes.
Avoiding Common Installation Mistakes
Avoid mistakes like inadequate depth, poor sealing, and improper insulation. These can lead to leaks, corrosion, and inefficiency. Thorough planning and careful execution can prevent these issues.
Maintenance Strategies
Adopt regular inspections, prompt leak repair, and timely insulation replacement. Use preventive measures like cleaning to minimize the risk of blockages. These strategies help maintain optimal performance.
Scheduled Inspections and Testing
Schedule regular inspections and testing for system efficiency, leak detection, and insulation integrity. This proactive approach allows early detection of potential issues, preventing costly repairs.
Prompt Repairs and Replacements
If issues arise, promptly repair or replace damaged components. Delay can exacerbate problems, leading to system inefficiency and possible environmental harm.
Conclusion
Proper installation and maintenance of underground refrigerant piping are crucial. From selecting the right materials and installation techniques to performing regular maintenance, each step plays a vital role in ensuring system efficiency.
The Importance of Proper Underground Refrigerant Piping
Proper refrigerant piping is vital to HVAC system efficiency and longevity. It aids in efficient refrigerant flow, reducing energy costs and ensuring a longer life for your system.
Key Takeaways for Successful Implementation and Maintenance
For success, select suitable materials, install properly considering depth and slope, avoid common mistakes, and conduct regular maintenance. Timely repairs and replacements are also essential for system longevity and efficiency.