Compressor efficiency test, ever heard of it? Perhaps not, but if you’re involved in industries that heavily rely on these mechanical marvels, this is your go-to phrase. It’s time we shed some light on this process, giving you the knowledge to unlock the full potential of your compressors. With that said, let’s set the wheels in motion.
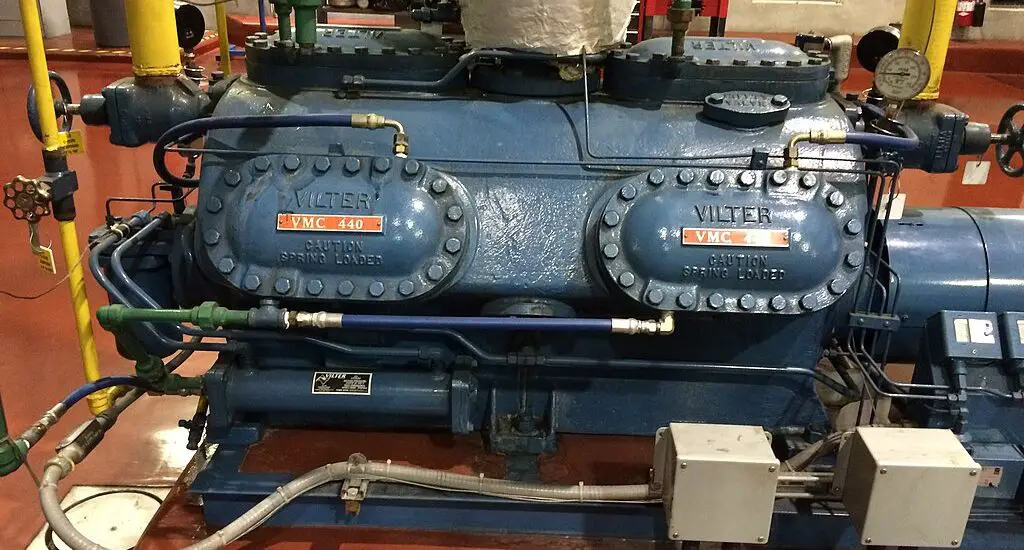
Table of Contents
Overview of Compressor Efficiency Testing
Simply put, a compressor efficiency test is a systematic process used to gauge how well a compressor is performing, squeezing every ounce of power from every drop of energy it uses. But why does it matter, you might ask? Well, stick around and we’ll break it down for you.
Importance of Testing Compressor Efficiency
Testing compressor efficiency is like going for a medical check-up. It helps spot issues before they balloon into full-blown problems. And, guess what? It saves you a pretty penny too. Think of it as a life jacket for your machinery. You hope you never need it, but you’ll be glad you have it when the time comes.
Understanding Compressor Efficiency
Compressor efficiency is the mechanical version of a magic trick. It’s about getting the maximum output with the least amount of input. In plain English, it’s about how much work your compressor does compared to the energy it consumes. It’s the secret sauce that makes all the difference.
Factors Affecting Compressor Efficiency
So, what’s the secret recipe for maximizing compressor efficiency? It’s a bit like baking a cake. The ingredients include operating conditions, maintenance frequency, and the type of compressor you’re using. Stir them up, and voila, you have the factors affecting compressor efficiency!
Common Efficiency Measures for Compressors
Measuring compressor efficiency isn’t a guessing game. There are precise ways to do it. Some folks use performance curves while others prefer looking at power per unit of output. Each has its charm and plays a vital role in keeping your compressor in tip-top shape.
How to Conduct a Compressor Efficiency Test
How is the efficiency test conducted you might ask, well, we’ve got the answer here.
Preparing for the Test
Running a compressor efficiency test isn’t something you do on a whim. It requires preparation. It’s like prepping for a marathon – there are steps to follow, equipment to check, and safety precautions to take. Let’s unravel these, shall we?
Safety Precautions
The world of compressors is not without its dangers. You’re dealing with moving parts, high pressures, and sometimes volatile substances. Safety first is the name of the game. It’s like the seatbelt in your car, you’ve got to strap in before you hit the gas.
Equipment Check
Now, let’s talk gear. Conducting a compressor efficiency test is akin to being a detective. You need the right tools to crack the case. From pressure and temperature gauges to power meters, you’ve got to have your tools in order to get an accurate reading.
Step-by-step Process of Testing Compressor Efficiency
Executing a compressor efficiency test isn’t rocket science, but it does require some technical know-how. Let’s get down to brass tacks and outline the step-by-step process. Buckle up, because we’re about to dive deep!
Starting the Compressor
The initial stage is all about bringing your compressor to life. It involves a set of steps as follows:
- Ensure that all connections are securely in place. Loose connections could lead to inaccurate results or even accidents.
- Check the oil and coolant levels. If they’re below the required level, refill them. They play a crucial role in the compressor’s operation.
- Turn on the power supply to the compressor. Ensure it’s connected to a stable power source to prevent power fluctuations.
- Start the compressor. It might have a start button or switch, depending on the model.
Monitoring and Recording Data
With the compressor humming along nicely, it’s time to play the observer. Here’s what you need to do:
- Monitor the pressure gauge. It shows the pressure level in the compressor. Note down the readings at regular intervals.
- Keep an eye on the temperature gauge. It indicates the operating temperature of the compressor. Record the temperature at the same intervals as the pressure.
- Use a power meter to measure the power consumption of the compressor. Jot down the readings.
- Calculate the compressor’s output by monitoring the flow rate. Most compressors have a flow meter for this purpose. Record the readings.
Shutting Down the Compressor
Once you’ve gathered all the necessary data, it’s time to wind things down. Here’s how:
- Press the stop button or switch off the power supply to halt the compressor.
- Close the outlet valve of the compressor to prevent any residual compressed air from escaping.
- Turn off the power supply to the compressor. This step ensures that the compressor won’t accidentally restart.
- Leave the compressor to cool down. This step is crucial, as compressors can get quite hot during operation.
Check out these other related articles…
Ice Machine Compressor Troubleshooting: Your Ultimate Guide
Refrigeration Compressor Tester: Your Comprehensive Guide
How to Reset Refrigerator Compressor: A Step-by-Step Guide
Refrigerator Compressor Sound Blanket: A Detailed Guide
Refrigeration Compressor Oil: Your Ultimate Guide
Decoding the Compressor Efficiency Test
Now that we have carried out the test and gathered data, the next step is to make sense of these figures. Here’s where we decode the results of our compressor efficiency test.
Analyzing Test Data
Looking at rows and columns of numbers can be daunting, but with a systematic approach, we can make it a walk in the park. Here’s how you can tackle it:
- Start by organizing your data. You can use a spreadsheet for this. Make columns for time, pressure, temperature, power, and flow rate, and fill them with the respective readings.
- Calculate the average pressure, temperature, power, and flow rate over the test period. This will give you a representative value for each parameter.
- Compute the volume of air compressed per unit time by multiplying the average flow rate by the duration of the test. This will give you the output volume.
- Calculate the input power by multiplying the average power reading by the duration of the test.
Understanding Test Results
Now, it’s time to interpret the results from the test data and assess the compressor’s efficiency. Here’s a step-by-step guide:
- Calculate the efficiency of the compressor using the formula: Efficiency = (Output Volume / Input Power) * 100. The result is expressed as a percentage.
- Compare the computed efficiency with the efficiency rating provided by the compressor manufacturer. This will give you an idea of how well your compressor is performing.
- If the efficiency is close to or equal to the manufacturer’s rating, your compressor is in good health. If it’s significantly lower, it might be time for maintenance or even a replacement.
- Repeat the efficiency test at regular intervals. Tracking efficiency over time can help you spot trends and address potential issues before they become serious problems.
A Peek into Refrigeration Compressor Efficiency Test
Refrigeration compressor efficiency tests come with their unique set of considerations. Let’s take a closer look at what makes these tests different and how to conduct them effectively.
Peculiarities of Refrigeration Compressor Efficiency
Refrigeration compressors are designed to handle refrigerants, not air, making the testing process a little different. Here’s why:
- Refrigerants have different physical properties compared to air. They’re denser and often operate at higher pressures. These differences must be accounted for during testing.
- The cooling load on the compressor varies, depending on the surrounding temperature and the temperature of the refrigerant. This adds another variable to the testing process.
- The efficiency of a refrigeration compressor is also influenced by factors such as heat exchange efficiency, the condition of the compressor’s seals, and the presence of any refrigerant leaks.
Conducting Efficiency Test on a Refrigeration Compressor
Given the unique aspects, testing a refrigeration compressor calls for a somewhat different approach. Here’s a step-by-step guide:
- Start by checking the refrigerant level in the system. It should be within the range specified by the manufacturer. If it’s too low, add refrigerant.
- Turn on the refrigeration system and allow it to reach a steady operating state. This may take a few minutes.
- Measure and record the temperature and pressure of the refrigerant at both the inlet and outlet of the compressor. Use these readings to determine the compressor’s actual cooling capacity using a pressure-temperature chart for the specific refrigerant.
- Measure the compressor’s power consumption using a power meter. Multiply this by the duration of the test to get the total energy consumed.
Analyzing Results of a Refrigeration Compressor Efficiency Test
Once you have gathered the necessary data, you can calculate the efficiency of your refrigeration compressor. Here’s how:
- Calculate the actual cooling capacity of the compressor using the formula: Cooling Capacity = (Outlet Temperature – Inlet Temperature) * Flow Rate * Specific Heat of the Refrigerant. The result will be in BTUs per hour or Watts, depending on your units.
- Calculate the compressor’s energy consumption during the test in kilowatt-hours (kWh).
- Finally, calculate the energy efficiency ratio (EER) using the formula: EER = Cooling Capacity / Energy Consumed. The result is in BTUs per hour per kWh for American units, or Watts per kWh for metric units.
- Compare your EER with the manufacturer’s specifications. A lower EER indicates less efficiency and might suggest the need for maintenance or replacement.