The heart of the refrigeration system, the compressor, leans heavily on the ‘refrigeration compressor lube oil properties’. These properties are not just a casual link but a lifeline to the compressor’s overall performance. They dictate the life expectancy, efficiency, and health of your compressor. Hang tight as we delve into the properties of the lube oil and understand why they’re so significant.
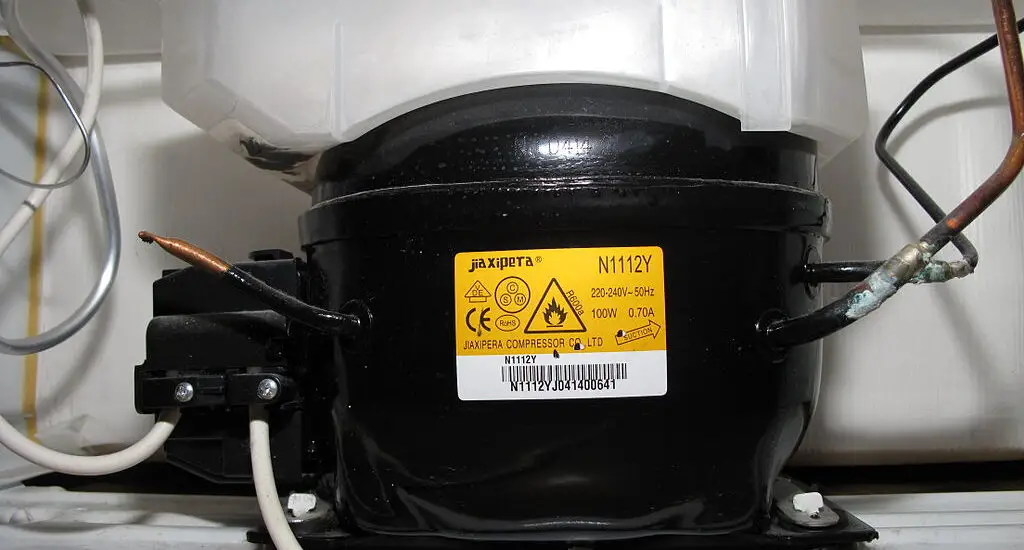
Table of Contents
Unfolding the Role of Lube Oil in Refrigeration Compressors
Lube oil is the unsung hero of a compressor, working behind the scenes to ensure everything runs smoothly. But what exactly does it do? Let’s have a closer look.
Embracing the Cool Factor: Cooling
In the harsh, heated world of the compressor, lube oil is the saving grace. It gracefully takes up the heat produced by the relentless mechanical processes, acting as a personal mini air-conditioner for your compressor’s components. It’s a cool job, but someone’s got to do it!
Sliding into the Role of Protector: Lubrication
If friction and wear are the villains in our story, lube oil is the valiant protector. It sweeps in between the compressor’s components, acting as a protective layer that reduces friction and slows down wear and tear. The result? A longer, healthier life for your compressor.
Keeping Things Tight: Sealing
Besides cooling and lubrication, lube oil plays a vital role in maintaining an effective seal within the compressor. It forms a seal between the piston and the cylinder wall, ensuring the refrigerant gas stays where it should. The lube oil is indeed a jack of all trades!
Dissecting Key Refrigeration Compressor Lube Oil Properties
What gives lube oil its superhero status? It’s the key properties. They determine how well it performs its role. So, it’s time to dig deeper.
Stickiness That Matters: Viscosity
Viscosity is the measure of a fluid’s resistance to flow – essentially, it’s ‘stickiness’. The right viscosity ensures that the lube oil can form a robust lubricating film between the compressor’s components, effectively reducing friction and dissipating heat. But here’s the catch – viscosity changes with temperature, which can impact the oil’s lubricating abilities. So, getting the viscosity right is a balancing act!
Staying Strong: Oxidation Stability
Over time, lube oil comes into contact with oxygen and heat, leading to oxidation – a process that can break down the oil and form sludge and acid. That’s where oxidation stability comes into play. The higher the oil’s oxidation stability, the better it can resist these harmful effects, ensuring your compressor runs smoothly for longer. So, it’s safe to say, oxidation stability is the lube oil’s endurance test.
Keep It Flowing: Pour Point
The pour point refers to the lowest temperature at which the oil remains fluid enough to flow. In cold conditions, lube oil can become too thick or even solidify, hindering its ability to lubricate the compressor’s parts. Hence, understanding the pour point is crucial for a compressor’s smooth operation, particularly in cooler climates.
Temperature’s Role in the Pour Point Drama
When it comes to pour point, temperature holds the reins. As the temperature drops, the lube oil becomes thicker – and if it gets too thick, it can’t lubricate the compressor’s parts effectively. This, in turn, can compromise the compressor’s performance and even lead to system failures. So, keeping an eye on the pour point and the operating temperature is critical for maintaining your compressor’s health.
Playing with Fire: Flash Point
Ever thought about the risk of fire in your refrigeration system? That’s where the flash point comes in. It’s the minimum temperature at which the oil vaporizes to form an ignitable mixture in the air. Keeping tabs on the flash point is crucial for ensuring the safety of your refrigeration system – it’s not something to be taken lightly!
Check out these other related articles…
Refrigeration Compressor Overheating: 3 Causes & Sure Fixes
Refrigeration Compressor Cycle: Your Ultimate Guide
Refrigeration Compressor HS Code: Your Ultimate 411 Guide
Refrigeration Compressor Tripping Breaker: 4 Sure Solutions
Refrigeration Compressor Capacity: A Practical Guide
Understanding Factors Influencing Refrigeration Compressor Lube Oil Properties
Refrigeration compressor lube oil properties aren’t set in stone – they can change based on a few factors. Let’s get to know these influencers a bit better.
The Root of It All: Quality of Base Oil
The quality of the base oil has a significant say in the overall properties of the lube oil. Higher-quality base oil typically has better oxidation stability and a lower pour point, leading to better performance and longevity of the compressor. It’s like choosing the best quality ingredients for a dish – it can make all the difference!
Adding the Extra Punch: Additives
Additives are the special ingredients that are added to enhance the oil’s properties. They work to improve oxidation stability, lower pour point, and even increase the oil’s resistance to wear. In other words, they help the lube oil to perform better and last longer. It’s like adding vitamins to your diet – they give you that extra health boost!
The Unwanted Guests: Contaminants
Contaminants are the uninvited guests in the world of lube oil. They sneak in during operation or maintenance, altering the oil’s properties and reducing its effectiveness. They can even lead to damage to the compressor. It’s essential to monitor and control contaminants to maintain the health of your compressor.
Evaluating Refrigeration Compressor Lube Oil Properties: A Peek into the Testing World
So, now that we know about these refrigeration compressor lube oil properties and what influences them, how do we measure them? Welcome to the world of lube oil testing.
Rating the Stickiness: Viscosity Index Testing
Viscosity index testing gives a measure of how much the oil’s viscosity changes with temperature. It’s like getting a report card on the oil’s lubricating performance across different operating conditions. It’s an essential test for selecting the right lube oil for your compressor.
Resisting the Breakdown: Oxidation Stability Testing
Oxidation stability testing assesses how resistant the oil is to oxidation over time. The higher the oxidation stability, the longer the oil will remain effective. This test is crucial for predicting the oil’s lifespan and ensuring the long-term health of your compressor.
Checking the Flow: Pour Point Testing
Pour point testing measures the lowest temperature at which the oil can still flow. It’s a critical test, especially if your compressor operates in cold conditions. The results can guide you in choosing the right oil for your specific climate.
Playing Safe: Flash Point Testing
Flash point testing checks the temperature at which the oil forms an ignitable mixture in air. It’s a vital safety test that can help prevent fire hazards in your refrigeration system. Safety first, after all!