When it comes to vapor compression refrigeration cycle problems and solutions, having a solid understanding can make all the difference in maintaining an efficient and reliable cooling system. Whether you’re a homeowner or an HVAC professional, this comprehensive guide will help you tackle common issues and keep your cooling systems running smoothly.
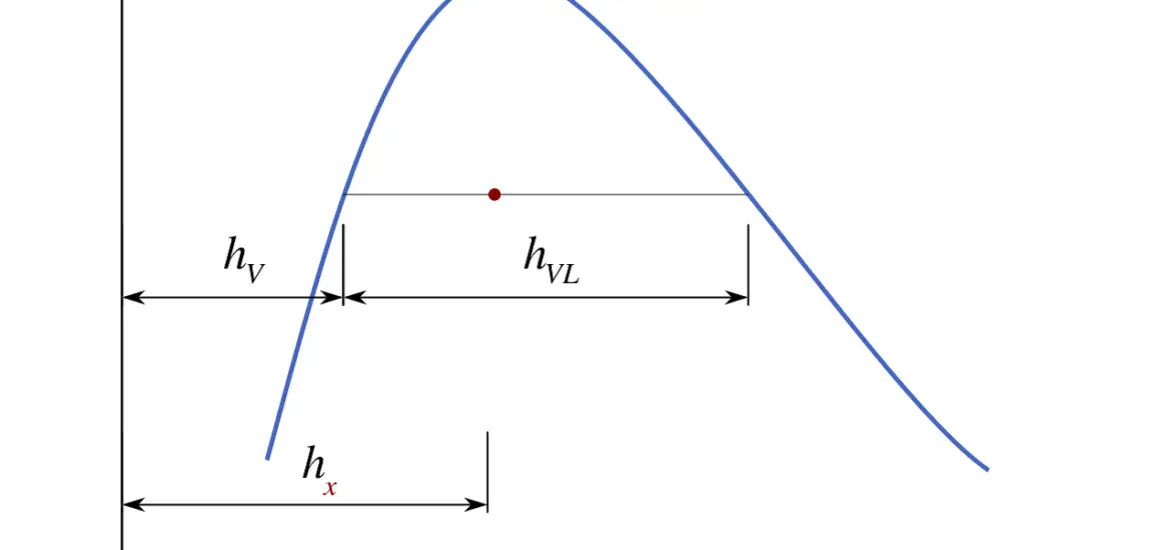
Table of Contents
Overview of the Vapor Compression Refrigeration Cycle
But first, let’s wrap our heads around the vapor compression refrigeration cycle itself. This process is the backbone of most cooling systems and involves a continuous cycle of heat transfer and phase changes.
Basic Components
The primary components include the compressor, condenser, expansion device, and evaporator. These parts work together in harmony to absorb heat and cool down your space.
General Operation Principle
Here’s how it works: the refrigerant starts as a low-pressure vapor, gets compressed into a high-pressure vapor, and then condenses into a high-pressure liquid. The expansion device turns the liquid into a low-pressure mixture, and the evaporator absorbs heat to create a cool environment. Sounds simple enough, right?
Common Applications of the Vapor Compression Refrigeration Cycle
This cooling method isn’t just for home refrigerators – it has a wide range of applications.
Domestic and Commercial Refrigeration
From your trusty fridge to commercial coolers, this process is vital for keeping food fresh and beverages chilled.
Air Conditioning Systems
Need a break from the summer heat? Air conditioning systems use this cycle to keep your home and office comfortable.
Industrial Refrigeration
Industries like food processing, pharmaceuticals, and chemical production rely on vapor compression refrigeration to maintain optimal temperatures for their products and processes.
Read our other vapor refrigeration articles – Vapor Refrigeration: Easy Guide to Keeping Things Chill
Common Problems in Vapor Compression Refrigeration Cycle
Unfortunately, even the best-designed systems can run into issues. Let’s explore some common problems that can crop up in vapor compression refrigeration cycles.
Compressor Issues
The compressor is the heart of the system, so problems here can be a real headache.
Overheating
Did you know that compressors can overheat? This can lead to a breakdown and damage other components. Keep an eye on the compressor’s temperature to avoid potential disasters.
Insufficient Oil Lubrication
Just like your car, the compressor needs proper lubrication to run smoothly. Without enough oil, you’ll run into friction, wear, and ultimately, failure.
Excessive Noise or Vibration
No one likes a noisy cooling system. Excessive noise or vibration can indicate an issue with the compressor, such as loose parts or misalignment.
Refrigerant Leaks
Got a refrigerant leak on your hands? This common problem can reduce efficiency and harm the environment.
Signs of Refrigerant Leaks
Keep an eye out for frost buildup, warm air blowing, or increased energy bills – these are all signs of a refrigerant leak.
Causes of Refrigerant Leaks
Leaks can result from corrosion, vibration, or faulty connections. Regular maintenance can help prevent these issues before they become costly problems.
Expansion Device Malfunctions
Problems with the expansion device can seriously impact your system’s cooling capacity.
Incorrect Expansion Valve Operation
An improperly functioning expansion valve can lead to inadequate cooling or even a complete system failure. Regular check-ups can help catch these issues early.
Blocked Capillary Tubes
Capillary tubes can become blocked by debris or ice, which hampers the flow of refrigerant. Keep these tubes clean to ensure optimal performance.
Evaporator and Condenser Problems
Issues with the evaporator and condenser can lead to a variety of cooling headaches.
Insufficient Heat Transfer
Poor heat transfer can stem from a dirty or damaged evaporator or condenser. Regular cleaning and maintenance can help keep these components in tip-top shape.
Frost Buildup
Frost can accumulate on the evaporator, which reduces heat transfer and cooling efficiency. Make sure to defrost your system periodically to keep it running smoothly.
Blocked Air Flow
Airflow is crucial for efficient cooling. Check for blockages or obstructions near the evaporator or condenser to maintain proper air circulation.
Solutions to Vapor Compression Refrigeration Cycle Problems
Now that we know the problems, let’s explore some practical solutions to keep your cooling system humming along.
Troubleshooting and Maintenance
Proactive maintenance and troubleshooting can save you time, money, and headaches in the long run.
Regular Inspection and Cleaning
Keep your system clean and clear of debris by scheduling regular inspections and cleanings.
Monitoring System Performance
Keep an eye on your system’s performance to spot potential problems before they escalate.
Periodic Replacement of Worn Components
Replace worn or damaged components as needed to maintain optimal performance and extend the life of your system.
Addressing Compressor Issues
Let’s tackle those pesky compressor problems head-on.
Ensuring Proper Oil Level and Lubrication
Check and maintain the oil level in your compressor to keep it running smoothly and avoid wear and tear.
Installing Temperature and Pressure Monitoring Devices
Monitor your compressor’s temperature and pressure to catch potential issues before they become full-blown problems.
Balancing and Alignment of Compressor Components
Ensure proper alignment and balance of compressor components to reduce noise, vibration, and wear.
Detecting and Repairing Refrigerant Leaks
Address refrigerant leaks quickly to maintain efficiency and protect the environment.
Leak Detection Methods
Use electronic leak detectors, UV dyes, or soap bubble tests to locate and fix refrigerant leaks.
Repair or Replacement of Leaking Components
Once you’ve found the leak, repair or replace the affected components to get your system back on track.
Fixing Expansion Device Malfunctions
Don’t let expansion device issues leave you in the heat.
Adjusting or Replacing Faulty Expansion Valves
Check and adjust your expansion valve settings or replace faulty valves to ensure proper refrigerant flow and cooling performance.
Clearing Blockages in Capillary Tubes
Clean out any debris or ice from capillary tubes to maintain optimal refrigerant flow and system efficiency.
Improving Evaporator and Condenser Performance
Keep your evaporator and condenser in top shape to maximize cooling efficiency.
Regular Cleaning and Defrosting
Clean and defrost your evaporator and condenser periodically to prevent frost buildup and maintain proper heat transfer.
Ensuring Proper Airflow
Check for obstructions and maintain proper airflow around your evaporator and condenser to optimize cooling performance.
Checking and Maintaining Refrigerant Charge
Regularly check and adjust your system’s refrigerant charge to keep it running at peak efficiency.
Preventative Measures and Best Practices
Prevention is better than cure, so let’s explore some preventative measures and best practices to keep your system running smoothly.
System Design and Component Selection
Choose the right components and design for your system to minimize potential issues.
Choosing Appropriate Refrigerants
Select environmentally friendly and efficient refrigerants that are compatible with your system.
Sizing Components Correctly
Ensure your system components are appropriately sized for your cooling needs to maximize efficiency and minimize wear.
Implementing Redundant Systems and Backup Components
Consider installing redundant systems or backup components to maintain cooling performance in case of component failure.
Operator Training and Awareness
Educate operators on proper system operation and maintenance to prevent issues and extend the life of your cooling system.
Understanding the Refrigeration Cycle and System Operation
Train operators to understand the refrigeration cycle and how each component contributes to efficient cooling.
Recognizing Early Warning Signs of Problems
Teach operators to recognize early warning signs of problems, such as abnormal noises or temperature fluctuations, and take appropriate action.
Proper Shutdown and Startup Procedures
Ensure operators follow proper shutdown and startup procedures to prevent damage and extend the life of your system.
Energy Efficiency and Environmental Considerations
Implement energy-efficient and environmentally friendly practices to minimize your cooling system’s impact on the environment.
Selecting Energy-efficient Components
Choose energy-efficient compressors, motors, and other components to reduce energy consumption and lower operating costs.
Implementing Heat Recovery Systems
Consider installing heat recovery systems to capture and reuse waste heat from your cooling process, further reducing energy consumption and costs.
Proper Refrigerant Handling and Disposal
Follow proper refrigerant handling and disposal procedures to minimize environmental impact and comply with regulations.
Conclusion
Understanding vapor compression refrigeration cycle problems and solutions is essential for maintaining efficient and reliable cooling systems. Regular maintenance, troubleshooting, and operator training can help prevent issues, extend the life of your system, and reduce its environmental impact. With these best practices in place, you’ll be well-equipped to keep your cooling system running smoothly for years to come.